Expo
ver canal
ver canal
ver canal
ver canal
ver canal
ver canal
Imagenología
Cuidados CriticosTéc. QuirúrgicaCuidados de Pacientes
Pruebas POCNegocios
Eventos
Webinars
- Microagujas inspiradas en el aguijón de abeja administran fármacos y estimulan la cicatrización de heridas
- Marcadores en sangre y patrones de ECG podrían ofrecer una alerta temprana de riesgos cardíacos ocultos
- Enfoque diagnóstico multidimensional identifica a pacientes con EPOC de alto riesgo
- Herramienta de IA predice marcadores de la enfermedad de Alzheimer
- Nuevo material flexible abre el camino a sensores portátiles autónomos
- La primera reparación de médula espinal humana con células del propio paciente podría curar la parálisis
- Nuevo trazador de doble modo permite a los cirujanos ver y escuchar el cáncer de próstata
- Implantación de cartílago cultivado del propio paciente acelera la curación tras la cirugía de cadera
- Sensor de diamante localiza cáncer metastásico para su extracción quirúrgica
- La reparación valvular mínimamente invasiva mejora la supervivencia en pacientes ancianos con IMFA
- Herramienta de capacitación en realidad virtual combate la contaminación de equipos médicos portátiles
- Plataforma de biosensores portátiles reducirá infecciones adquiridas en el hospital
- Tecnología portátil de luz germicida, única en su tipo, desinfecta superficies clínicas de alto contacto en segundos
- Solución de optimización de la capacidad quirúrgica ayuda a hospitales a impulsar utilización de quirófanos
- Innovación revolucionaria en esterilización de instrumentos quirúrgicos mejora significativamente rendimiento del quirófano
- Medtronic se asocia con Corsano para ampliar su portafolio de atención aguda y monitorización en Europa
- Colaboración ampliada transformará la tecnología en quirófanos mediante IA y automatización
- Boston Scientific adquiere la empresa de dispositivos médicos SoniVie
- Teleflex adquirirá el negocio de intervención vascular de BIOTRONIK
- El Congreso Mundial de Hospitales de 2026 se celebrará en Seúl
- Los relojes inteligentes podrían detectar la insuficiencia cardíaca congestiva
- Un parche inteligente versátil combina monitoreo de salud y administración de fármacos
- Modelo de aprendizaje automático mejora predicción del riesgo de mortalidad para pacientes de cirugía cardíaca
- Colaboración estratégica para desarrollar e integrar IA generativa en el cuidado de la salud
- Solución de quirófanos habilitada para IA ayuda a hospitales a maximizar la utilización y desbloquear la capacidad
- Sistema de hemostasia de sangre total POC de última generación reconoce necesidades específicas de servicios de emergencia y quirófanos
- Laboratorio portátil permitirá identificación de infecciones bacterianas más rápida y económica en el punto de necesidad
- Mercado mundial de pruebas de cabecera será testigo de perspectivas prometedoras en cuidados intensivos
- Mercado mundial de diagnóstico de sepsis impulsado por el aumento de enfermedades adquiridas en hospitales
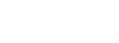
- Microagujas inspiradas en el aguijón de abeja administran fármacos y estimulan la cicatrización de heridas
- Marcadores en sangre y patrones de ECG podrían ofrecer una alerta temprana de riesgos cardíacos ocultos
- Enfoque diagnóstico multidimensional identifica a pacientes con EPOC de alto riesgo
- Herramienta de IA predice marcadores de la enfermedad de Alzheimer
- Nuevo material flexible abre el camino a sensores portátiles autónomos
- La primera reparación de médula espinal humana con células del propio paciente podría curar la parálisis
- Nuevo trazador de doble modo permite a los cirujanos ver y escuchar el cáncer de próstata
- Implantación de cartílago cultivado del propio paciente acelera la curación tras la cirugía de cadera
- Sensor de diamante localiza cáncer metastásico para su extracción quirúrgica
- La reparación valvular mínimamente invasiva mejora la supervivencia en pacientes ancianos con IMFA
- Herramienta de capacitación en realidad virtual combate la contaminación de equipos médicos portátiles
- Plataforma de biosensores portátiles reducirá infecciones adquiridas en el hospital
- Tecnología portátil de luz germicida, única en su tipo, desinfecta superficies clínicas de alto contacto en segundos
- Solución de optimización de la capacidad quirúrgica ayuda a hospitales a impulsar utilización de quirófanos
- Innovación revolucionaria en esterilización de instrumentos quirúrgicos mejora significativamente rendimiento del quirófano
- Medtronic se asocia con Corsano para ampliar su portafolio de atención aguda y monitorización en Europa
- Colaboración ampliada transformará la tecnología en quirófanos mediante IA y automatización
- Boston Scientific adquiere la empresa de dispositivos médicos SoniVie
- Teleflex adquirirá el negocio de intervención vascular de BIOTRONIK
- El Congreso Mundial de Hospitales de 2026 se celebrará en Seúl
- Los relojes inteligentes podrían detectar la insuficiencia cardíaca congestiva
- Un parche inteligente versátil combina monitoreo de salud y administración de fármacos
- Modelo de aprendizaje automático mejora predicción del riesgo de mortalidad para pacientes de cirugía cardíaca
- Colaboración estratégica para desarrollar e integrar IA generativa en el cuidado de la salud
- Solución de quirófanos habilitada para IA ayuda a hospitales a maximizar la utilización y desbloquear la capacidad
- China aprueba la primera vacuna inhalable contra la COVID-19 del mundo
- Vacuna en parche contra la COVID-19 combate variantes del SARS-CoV-2 mejor que las agujas
- Pruebas de viscosidad sanguínea predicen riesgo de muerte en pacientes hospitalizados con COVID-19
- ‘Computadora Covid’ usa IA para detectar COVID-19 en exámenes de TC de tórax
- Técnica de resonancia magnética muestra la causa de los síntomas de COVID prolongada
- Sistema de hemostasia de sangre total POC de última generación reconoce necesidades específicas de servicios de emergencia y quirófanos
- Laboratorio portátil permitirá identificación de infecciones bacterianas más rápida y económica en el punto de necesidad
- Mercado mundial de pruebas de cabecera será testigo de perspectivas prometedoras en cuidados intensivos
- Mercado mundial de diagnóstico de sepsis impulsado por el aumento de enfermedades adquiridas en hospitales